The Amazing Sculptures of Nano Lopez: From Clay to Bronze
Like most artists, Nano Lopez begins the creation of a new work of art with the stroke of a pencil. (You can see a look at his complete process in the video above.)
Lopez begins the intensive process of creating a sculpture by sketching it. From those drawings he makes a clay model that serves as the original.
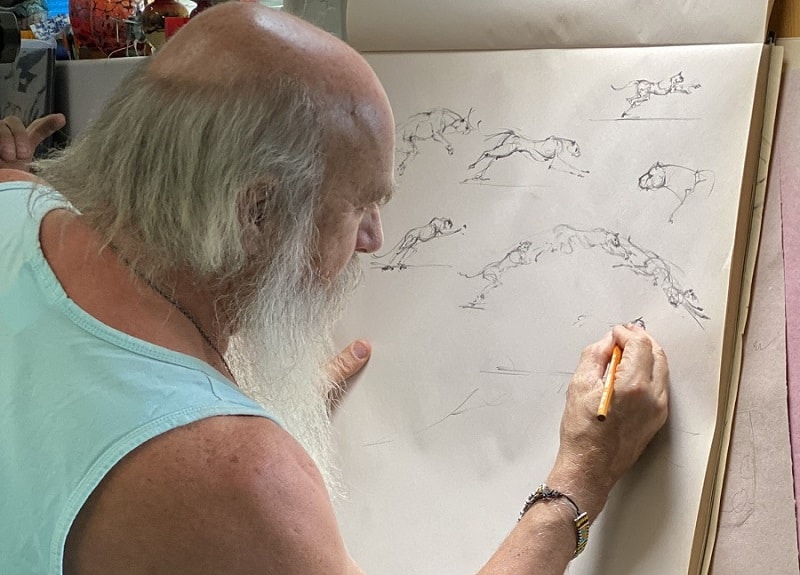
Nano starts with a sketch…
When the anatomy is to his liking, he adds organic and mechanical textures to the clay model as well as letters, gears or buttons. All details the artist wants on the final product must be on this model.

… and then brings that sketch to life with clay.
Creating a Mold
The sculpture is coated with multiple layers of silicone, using air blow guns to ensure all details are covered. Once dry, the silicone-coated model is encased in a thick plaster or fiberglass mixture to hold the pliable silicone in place. This is known as the “mother mold.”
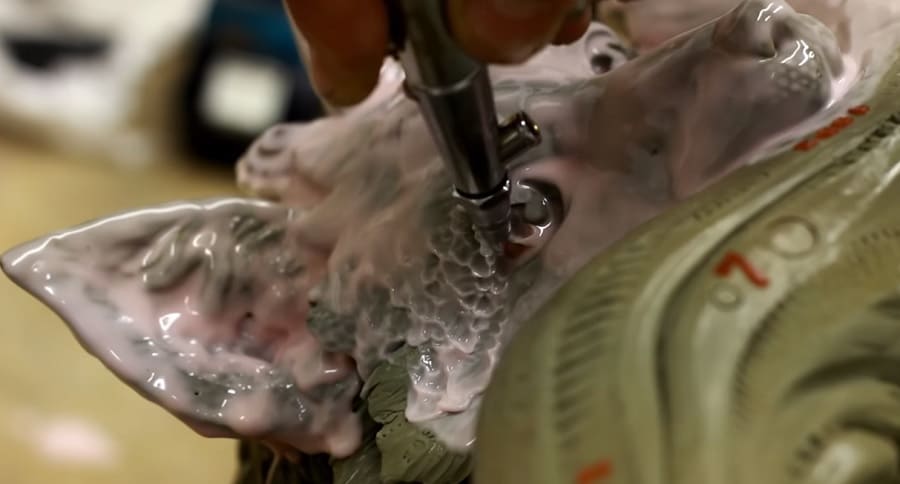
Several coats of silicone are applied to create a mold. Here, silicone is used to cover a clay model of Lopez’s iconic “Foxy” sculpture.
After the mother mold hardens it is opened and separated. The original model is removed from the silicone, and by closing the two halves of the silicone, a mold is formed to create an exact “negative” of the clay model.
Melted wax is poured into the rubbery mold, thoroughly coating it so all the intricate details are captured. Once the wax has cooled, this wax “positive” is removed from the mold, and any imperfections in the wax are fixed. A wax gating system is then installed on the wax sculpture. These wax spruces provide channels that the molten bronze will travel through.
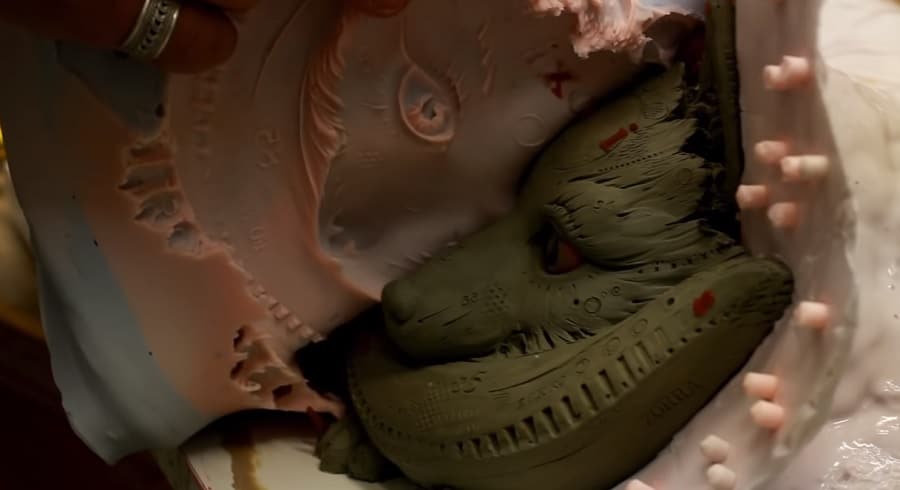
The original clay mold (Foxy, in the above image) is removed from the silicone mold.
The Ceramic Shell
The gated wax sculpture is coated in liquid ceramic slurry, then immediately covered in sand to help the slurry breathe. These two steps are repeated until there is nearly half an inch of a hard, ceramic shell encasing the wax.
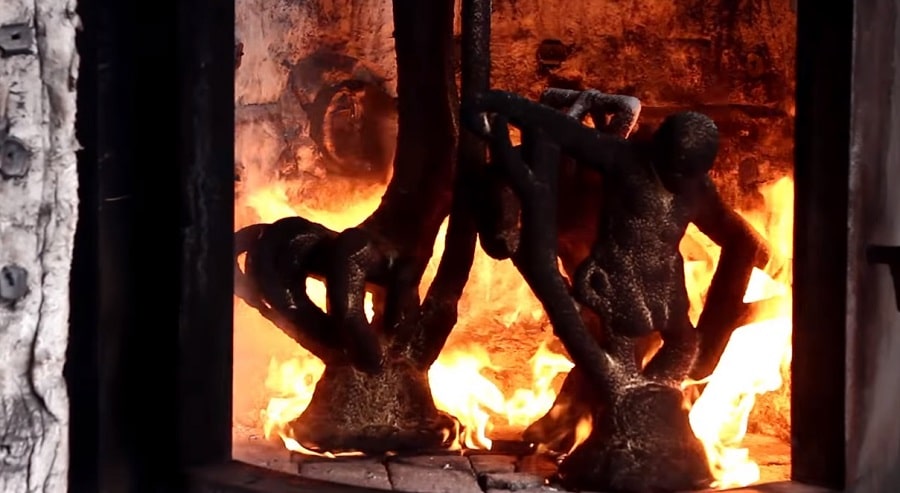
Wax leaving the ceramic shells in the kiln gives the “lost wax” sculpting technique its name.
The ceramic “cap” on the bottom is removed and the shell is placed in a kiln. The “lost wax” technique receives its name from this step due to the wax melting out of the shell.
Begin the Bronzing
The melted bronze (about 2,100 degrees Fahrenheit) is then poured into the empty ceramic mold. Once it cools down, the ceramic shell is removed with pneumatic hammers and sandblasting. The metal chasing starts with large grinders to remove any large pieces of unwanted metal, such as the gates, then more refined tools are used to re-create the textures found on the original.
If the sculpture is made up of multiple pieces, they are welded together and the weld lines are smoothed over.
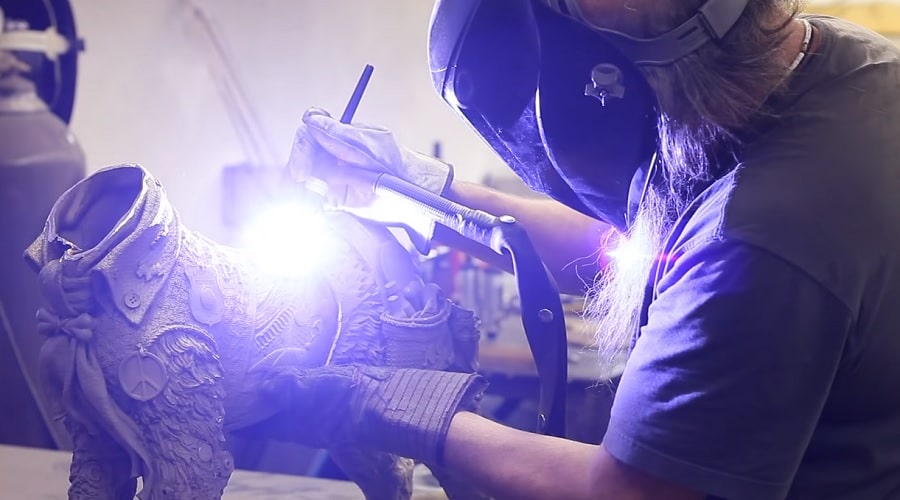
Nano Lopez welds together the bronze pieces of one of his sculptures.
Coloring Metal
For Lopez, coloration begins by heating the sculpture and spraying it with a chemical that turns it black. The sculpture is sanded, making the surface smooth and shiny while leaving black in recesses to accentuate the textures.
A gold dye is sprayed onto the sculpture. From there, patinas made of chemicals and pigments are applied with a brush and torch. By heating the bronze, the colors are essentially “cooked” onto the metal.
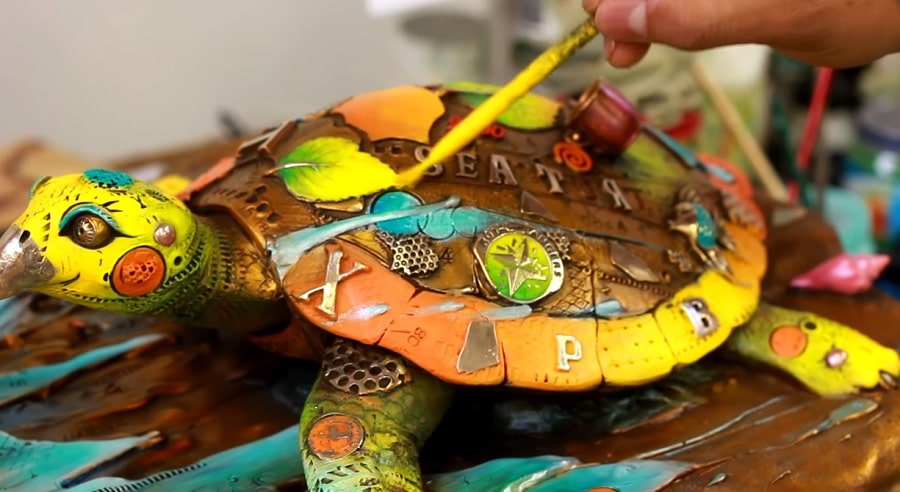
Patinas are hand-painted into the sculptures and then cooked on with a blowtorch.
Finally, a few coats of lacquer are sprayed onto the sculpture to protect it from wear-and-tear and UV rays. If needed, felt is attached to the bottom of the sculpture.
As Lopez says, “That’s the end of the process.”
To learn more about how you can reserve one of Lopez’s made-on-demand sculptures, contact our gallery consultants at (800) 521-9654 ext. 4 or sales@parkwestgallery.com.
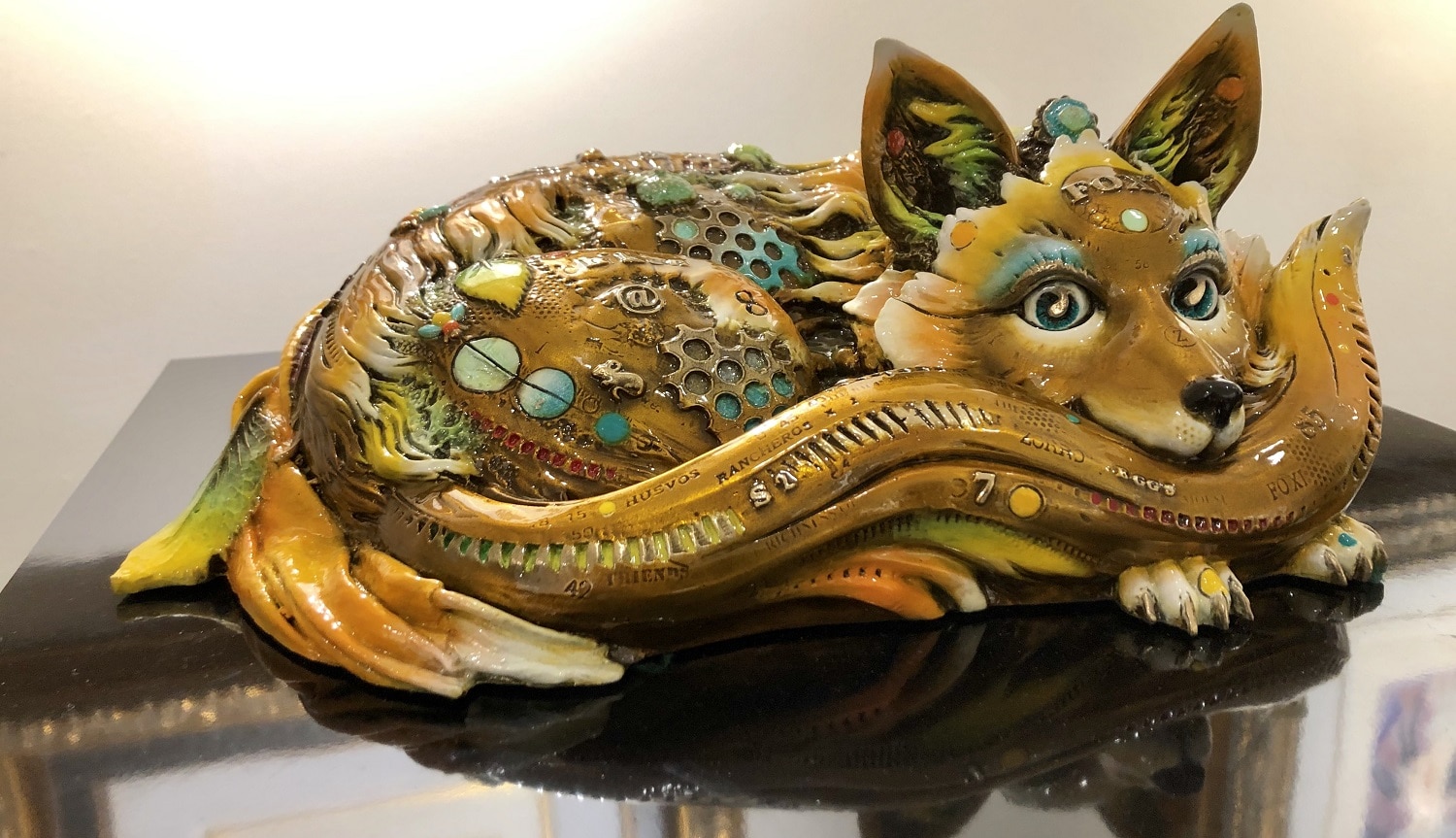
“Foxy” (2017), Nano Lopez
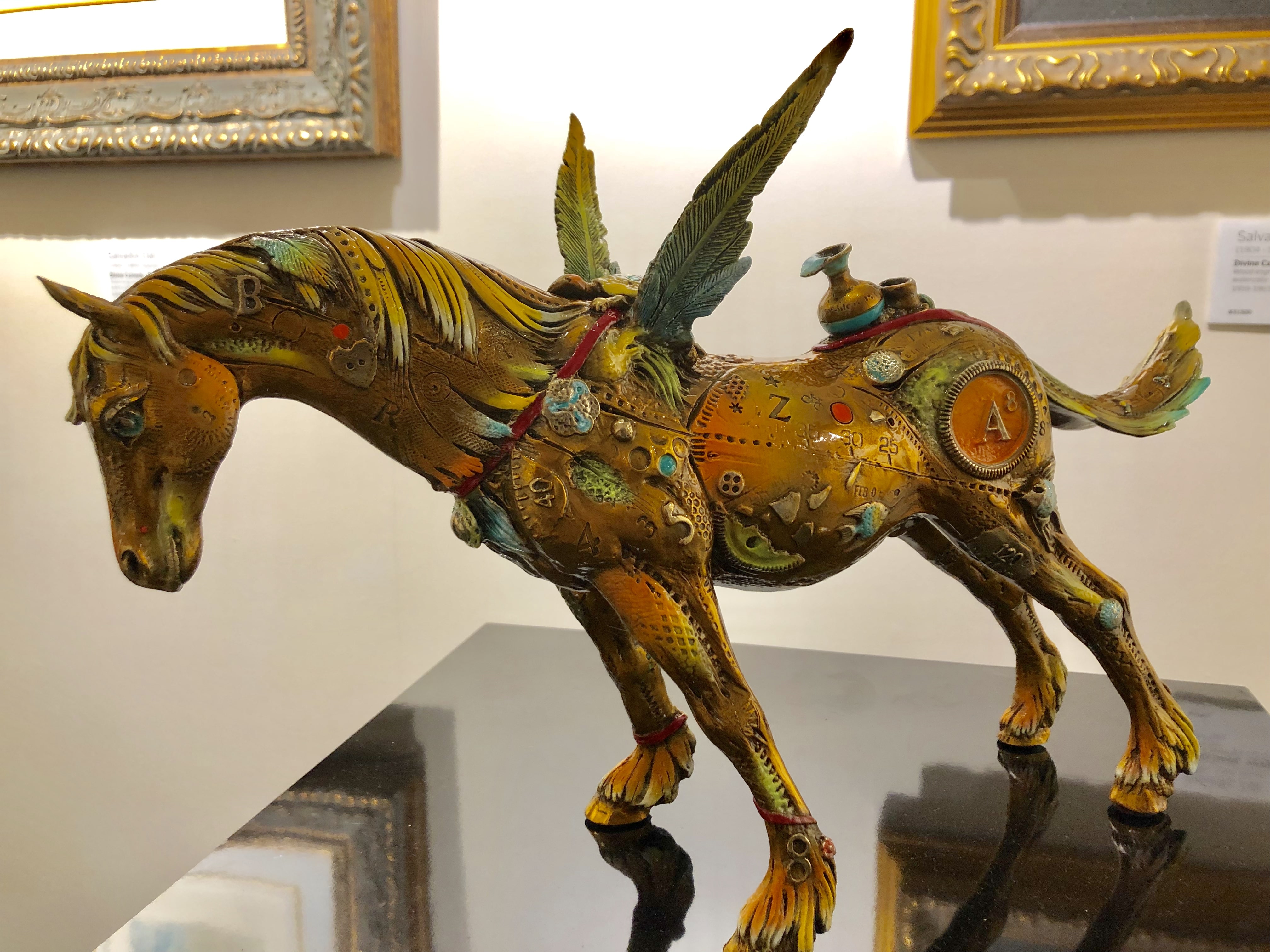
“Arthur the Believer” (2017), Nano Lopez
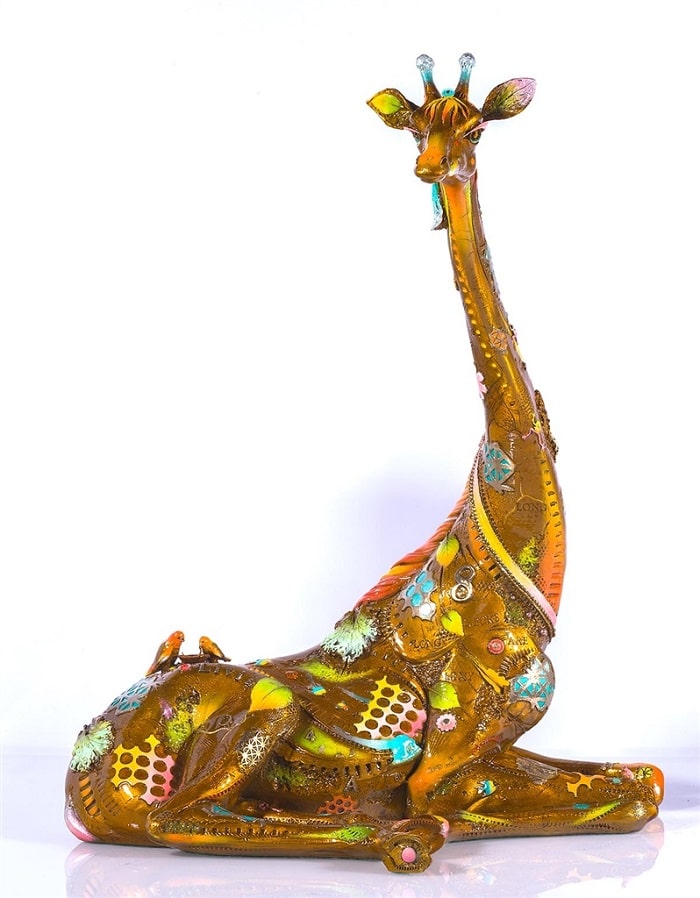
“Olivia” (2017), Nano Lopez